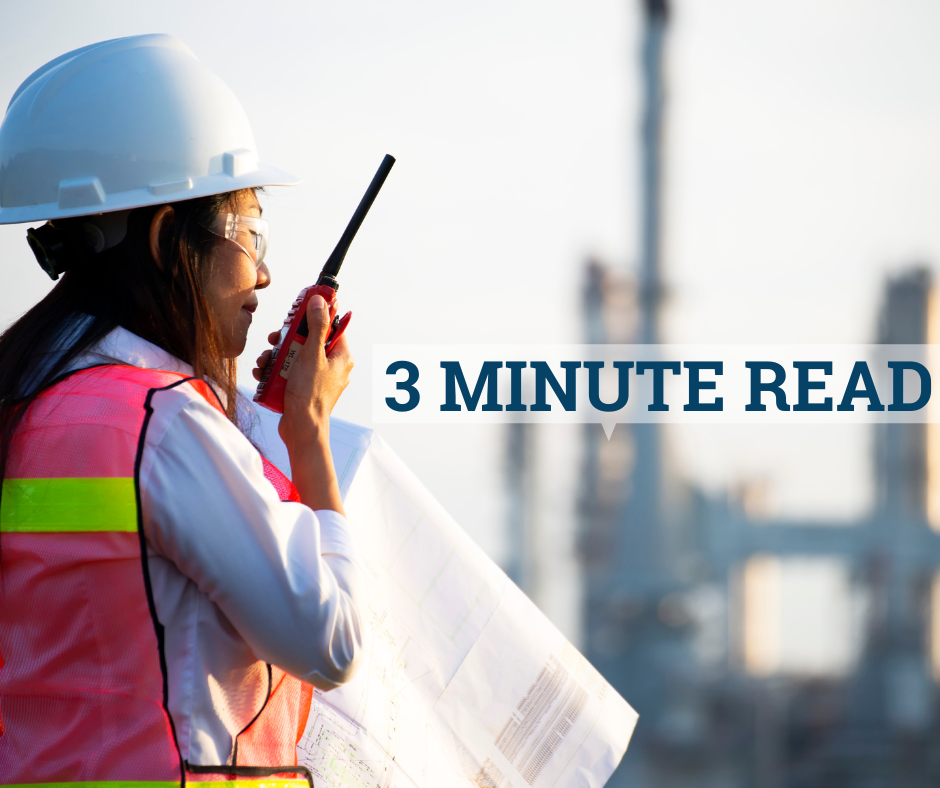
Workplace safety and health hazards are serious concerns that can significantly impact employees and a company's overall operations. Recently, Dana Container, a transportation company in New Jersey, has come under scrutiny for repeatedly failing to address safety hazards, resulting in hefty fines imposed by the Occupational Safety and Health Administration (OSHA).
Background
Dana Container, located in Paulsboro, New Jersey, has been facing a substantial fine of $437,860 from OSHA due to various workplace safety and health hazards involving chemicals. The investigation was initiated in July 2023 following an employee complaint highlighting significant safety and health deficiencies within the company.
The OSHA investigation revealed several violations, including a willful violation for the improper maintenance of safety data sheets for chemicals, such as corrosives. In addition, the company was cited for three repeat violations, including failure to update container labels, inadequately maintained eyewash stations, and a lapse in conducting medical evaluations for workers before respirator use. Dana Container had also been cited for similar violations in 2019 and 2023, indicating a recurring pattern of non-compliance.
Furthermore, the company received four serious citations for failure to inspect hoists, establish a written hazard communication program, and ensure the fulfillment of safety requirements while using a lifeline fall protection system.
The company has been given 15 business days to either comply with or contest the findings. Dana Container must rectify the identified safety and health hazards and implement robust measures to prevent their recurrence in the future.
Importance Of Compliance And Accountability
The repeated nature of these violations raises serious concerns about Dana Container’s commitment to ensuring the safety and well-being of its employees. Workplace safety is a legal obligation and is imperative for companies, especially those involved in transporting and handling hazardous materials.
Ensuring a safe working environment is crucial for safeguarding the welfare of employees and preventing potential accidents or long-term health issues resulting from exposure to hazardous chemicals. In addition, non-compliance with safety regulations can tarnish the company's reputation, leading to a loss of trust among employees, clients, and the public.
Embracing A Culture Of Safety
Dana Container should consider reevaluating its safety protocols, providing thorough training to employees on chemical handling and safety procedures, and implementing stringent measures to ensure compliance with OSHA regulations. This serves as a reminder of the importance of upholding workplace safety and health standards, particularly in industries dealing with hazardous materials.
Consider partnering with a professional employer organization (PEO) like GMS to ensure the safety of your employees. GMS works with a wide variety of industries, including the transportation industry. As your transportation and logistics company grows, the administrative aspects of your business require more time and resources. Our safety experts help business owners take a proactive approach to workplace safety through various services. These strategies include:
- Training
- Job hazard analysis (JHA) and standard operating procedures (SOP)
- Onsite consultingÂ
- OSHA inspection and citation assistance
- Jobsite inspections
- Accident and injury investigations